FCCL、島根富士通の現場に宿る「人を想うモノづくり」
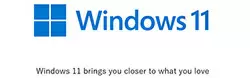
富士通クライアントコンピューティング(FCCL)のPCは、使う人にハードが寄り添う「人を想うモノづくり」というコンセプトに基づいてつくられている。その思想は、FCCLのFMVシリーズのノートPCやデスクトップPC、タブレット端末、法人向けBTOモデルを含むすべての製品の製造を担う島根富士通にも徹底して浸透している。工場で働く約1300人の一人ひとりが、顧客のことを想いながら現場の改善をモノづくりに反映することで、CS(顧客満足度)の高いMade in Japan品質を保っている。「人を想うモノづくり」の現場をレポートする。
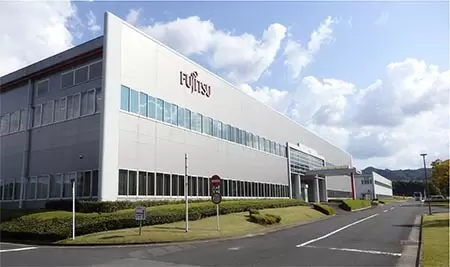
世界最軽量の約634gは島根から生まれた
「人を想うモノづくり」という理念に基づいてFCCLが開発・設計したPCの製造を担うのが、島根県出雲市の田園風景が広がる高台に生産拠点を構える島根富士通である。1990年の創業から31年目となる同社は、コンシューマ向けFMVを発売当初より製造しており、5世代目となる世界最軽量モデルであるFMV LIFEBOOK UHシリーズは、初代からこの島根でつくられている。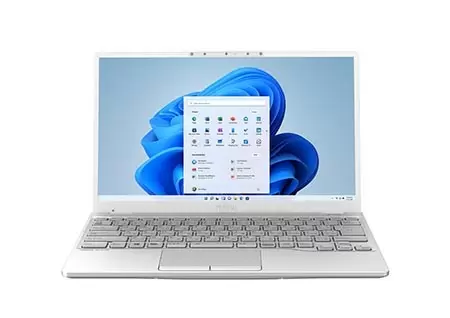
初代モデルから島根富士通で製造している
また、17.3型の大画面液晶を搭載するFMVのNHシリーズは、従来は海外で生産していたが今回、島根富士通にラインを新設して国内生産体制に移管した。コロナ禍の最中でのグループを挙げた大きな事業改革だったにもかかわらず、社員の感染はもちろん、操業停止やトラブルに見舞われることなく、減産することもなかった。高い技術力や生産管理能力があったからこそなせる業で、このことにもっとスポットライトが当てられてもいいだろう。
21年4月、現場たたき上げのプロパーとして新社長に就任した神門明(こうど・あきら)氏は国産へのこだわりを次のように語る。「生産性を高めるのはもちろん、一人ひとりがお客様のことをどれだけ想ってつくれるかが大切。Made in Japan品質をお客様にお届けするんだというミッションの元、R&Dと連携しながら軽量、堅牢、快適なキーボードの打感などを追い求めている。そうした日々の積み重ねで実現したのが、UHシリーズの約634gだ」と、世界最軽量モデルはFCCLと連携した国産品質があったからこそ生まれたと語る。
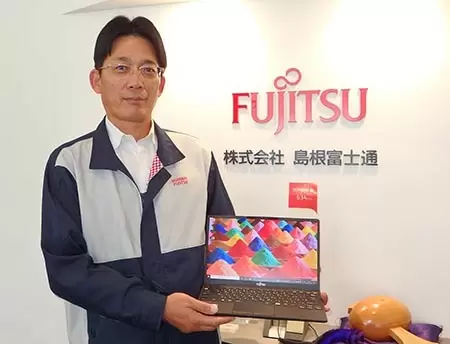
「人を想うモノづくり」を浸透させる仕組み
コストだけを考えれば海外で生産した方がいいはず。Made in Japanにこだわる理由について神門社長はさらに「細かい部品の品質や作り込みの品質、人と機械が協調した安定品質など、日本でつくる安心感をお客様にお届けするには国内製造にこだわる必要がある」と語る。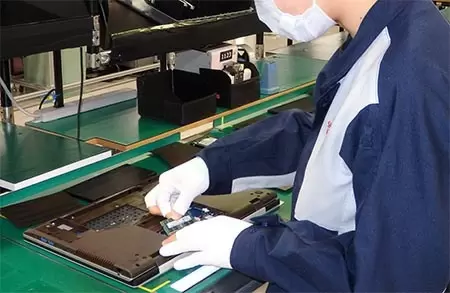
NHシリーズのライン
人を想うモノづくりの思想は、社員の教育制度にも反映することで、実際の製造現場の隅々にまで浸透する。例えば、製造ラインでいつもと少しでも違うことがあれば、一人ひとりが報告する活動を「CS貢献賞」として表彰している。製造の現場では小さな課題が少なからずある。完成品に貼るラベルのレイアウトが少しずれる、部品の色味が異なるなど、些細なズレやいつもとは違うことを気づいた人に、社内表彰で称える。
「他にも品質のスペシャリスト育成教育やQC活動などを通じて、生産性を上げるだけでなく、ベースとなる品質を高めながら、当たり前のように作り込める人材を育てている。これらのことすべてがMade in Japan、Made in 島根の品質につながる。モノをつくる一人ひとりの気持ちがお客様を想わない限り、いいものがつくれるはずがない。われわれはこれを“モノづくりのDNA”と呼んでいる」。
アフターフォローに欠かせない修理部隊も工場に常駐する。製品に少しでも不具合があれば工場で診断・分析し、その結果をR&Dやモノづくりの現場にフィードバックするサイクルを循環させることで、モノづくりの品質はさらに高まる。
ノートPCやタブレットの基板製造から組み立て、修理まで一貫して担う島根富士通だからこそできる、CS向上のための仕組みと言えるだろう。
島根富士通ではFMVのノートPCなど約20機種のほか、BTOの法人向けPCも手掛け、月産25万台の能力を誇る。稼働時間は8~17時で平日の月~金なので、営業日で単純計算すると1日当たり1万台となる。
日産1万台といっても今の時代、大ロット、大量生産でないことはもちろん、もはや小ロット、多品種生産ですらない。「変種変量」と称するように、扱う機種も変われば数量も常に変動する。
ここで簡単に工場内の工程を説明すると、1階は、プリント板製造の「全自動一貫ライン」となっており、基板への半田印刷や部品実装は全て自動で行われる。出来上がったメインボードは、2階まで自動搬送ロボットが運び、ラインで人がディスプレイなどの部品を組み立てて完成品にする。この人が組み立てるラインに、異なる3機種を1台ずつ交互に生産することにより「変種変量」に対応している。
ライン数は25あり、そのうちデスクトップPCは4ライン。ほとんどがノートPCやタブレットとなる。社員数は約600人、協力会社の社員が約700人の合計約1300人がモノづくりに携わる。
スマートファクトリー化の最前線
さて、通信ネットワークが高速、大容量化する5G時代に突入し、モノづくりの現場にもICTやIoTを導入する動きが加速している。島根富士通でも、そんなスマートファクトリー化に取り組んでいる最中だ。神門社長は現在の進捗状況について「完全スマート化までの三つのステップがあるとすれば、今は第一ステップ。試験のログや搭載部品のロット情報、どの工程でどの人が何本ねじを締めたかなど、モノ、人、設備のあらゆるデータを抽出する作業に取り組んでいる。今のところ、ほしいデータの85%を取得できるところまで進んだ」と、第一ステップの手ごたえを感じている。
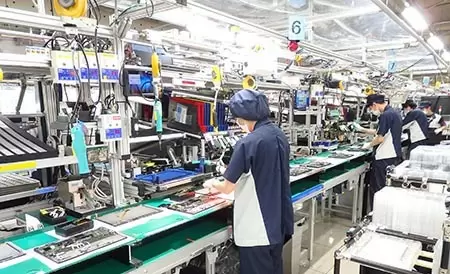
実際の工場内をのぞいてみると、組み立てラインの斜め上にねじ締め本数を計測するカウンターが設置してあるのがわかる。ねじが締まるたびに数字は減り、ねじの締め忘れがないかが一目でわかる。その他にも作業の遅れや異常の際、作業者自ら管理者を呼ぶスイッチがあり、そのデータを集約しモニターで可視化することで、さらなる改善活動につなげる。ねじ1本でも、よりよいモノづくりに反映させるための貴重なデータというわけだ。
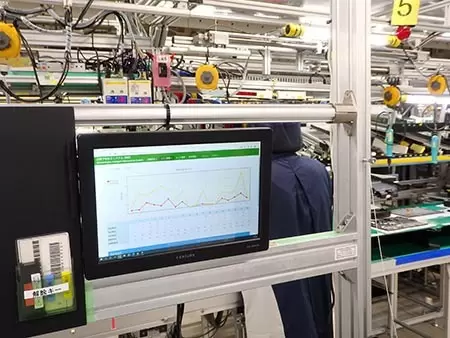
また、組み立てに必要な部品のロケーションは、緑のランプの点灯で示される。前述したように、ラインにはシリーズの異なる3機種が流れてくるので、機種ごとに異なる部品を取り付けなければならない。部品をピックアップすればランプは消えるので、取り付け忘れがないかを確認できる。こうした一つひとつのデータも徹底して抽出する。
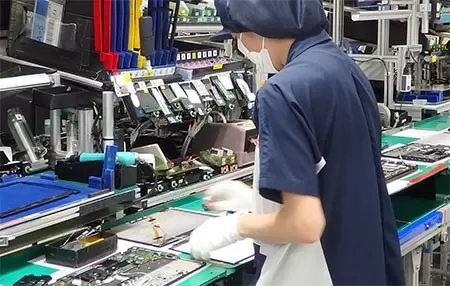
工場内で抽出されたあらゆるデータは、独自構築したプラットフォームである「データ分析基盤」に入れ、いつもとの違いやバラつき、人の動きの変化点、設備のメンテナンス周期などの分析に役立てている。
ここから先は、第二、第三ステップとして今後の取り組みとなる。AIであたりをつけるのか、それともAIでディープラーニングしたものを、これまでの人の知見とミックスさせるのかなど、どのようなアルゴリズムで運用するかを手探りで模索している段階という。
また、1日に何万というデータトラフィックがある中、必要なデータだけをエッジコンピューティングで絞ってから吸い上げるなど、検討すべき項目は尽きない。「ハードとソフト、人のいずれかだけが尖っていてもダメで、すべてが協調しながらバランスよく進化させていかなければならない」と、神門社長はスマートファクトリー化を進める上での肝を語る。
デジタルとアナログが融合する現場
ここまで社員制度や人が作業するラインを見てきたが、工場でもう一つ見逃せないのが自動化の取り組みである。例えば、世界最軽量モデルのUHシリーズのキーボードの裏には70本のねじが取り付けられるが、ねじ1本のサイズは径1.4ミリ、長さ1.5ミリという小ささ。ねじの頭にドライバーの十字が刻まれているのが目視で確認できないほど小さい。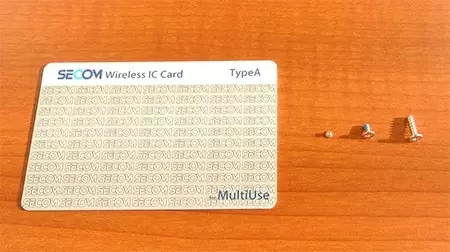
(径1.4ミリ×長さ1.5ミリ)
このようなねじはとても人手で締められるものではないため、専用ロボットを独自開発した。ずらりと12台並んだ専用ロボットが、この極小ねじを空気で吸引しながら次々と素早く正確に締めていく。これは自動化の一例である。
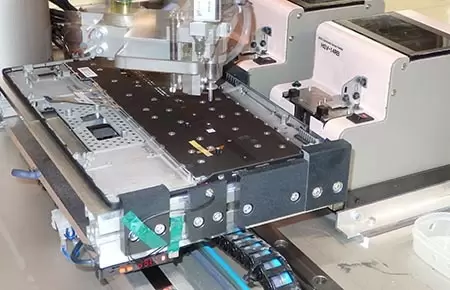
他にも自動化については、1階にずらりと並ぶ全自動一貫ラインが代表的なものだ。プリント基板にはんだを印刷した後、リールに巻かれたコネクタやコンデンサなどの小さなチップが、部品実装機でプリント基板に実装される。その後、200℃以上の高温ではんだを溶かすリフロー炉で、部品とはんだを固定してメインボードが出来上がる。
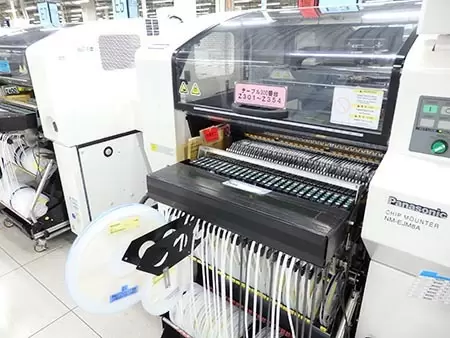
プリント基板に部品が実装されていく間には、関所のような箇所が設けられ、部品が正確に実装されているかを画像検査機で識別する。また、自ら治具を取り替えてプリント基板の方向を変えたり、組み立てたりするアーム型の垂直多関節ロボットも活躍する。
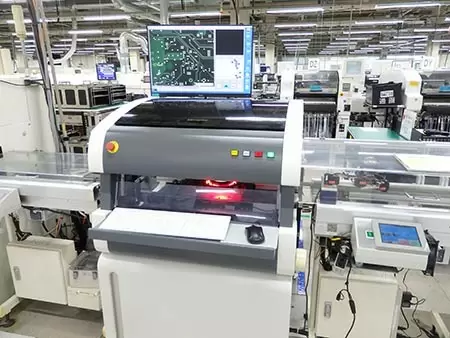
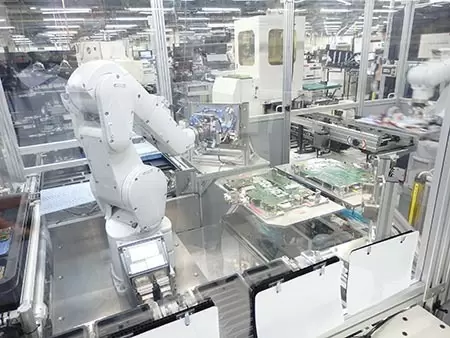
こうして全自動一貫ラインで組み立てられたメインボードは、先述した自動搬送ロボットで2階のラインに運ばれる。島根富士通の工場内で最初に目につくのが、流行りのメロディーを軽快に鳴らしながら工場内を動き回る無人搬送ロボットだ。
エレベーターでは、信号を送受信しながらドアの開閉やボタンを自ら操作して無人で搬送する。ちなみに、エレベーターは搬送ロボット専用ではなく、人が乗るときは搬送ロボットが止まり待機している。
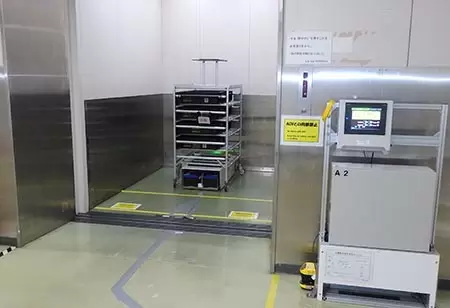
神門社長は「これまで基板や部品の搬送に4人かかっていたところ、すべて搬送ロボットで自動化するようにした。基本的に工場内の物流は自動化している」と説明する。単純作業はロボットに任せ、人はより高度な技術が求められる作業に携わるように工夫している。
島根富士通では「人と機械の協調生産」と呼んでいるように、お客様のことを想いながらつくる人と、それをサポートするロボットが、まさに協調しながらモノづくりをしている様子がわかる。ラインの工程の一つひとつに「人を想うモノづくり」の思いが宿り、それが一つの完成品となって市場に出荷されていくのだ。