認知症リスクの要因の一つとしてもあげられている「難聴」は、高齢化が進行する日本では、国民病として認識され始めている。しかし、その対策として多くの人がイメージするであろう補聴器の日本での使用率は世界でもワーストクラスだ。今回、少しでも補聴器の世界を知るために、世界でも有数の補聴器メーカーであるオーティコン補聴器のあまりお目にかかることのない製作現場を取材した。
あまりお目にかかる機会のないオーティコン補聴器のラボに潜入
今回取り上げるのは耳あな型。すっぽりと耳の内部にフィットさせるために事前に耳型を採型する
耳型採型は、補聴器を自分の耳に完璧にフィットさせるために行う。装着感はもちろんだが、音を明瞭に聞き取るという目的を達成するためには音の出力口がまっすぐ鼓膜を向いていなければならない。したがって、耳あな型の補聴器は目に見えている表面だけではなく、鼓膜へと続く外耳道まで型をとる。
耳型は外耳道まで採型する必要がある(写真は耳の構造模型)
手順としては、まず耳の中を拡大鏡やペンライトで観察する。異常がなければ、次は外耳道の奥に綿球を入れ、耳型の元となる印象材(シリコン樹脂)が耳の奥に入らないように栓をする。今回、印象材は主材と硬化剤の2種類を混ぜ合わせたものを使用した。単体では粘土のような柔らかさだが、混ざると徐々に硬化していく。固まる前にシリンジと呼ばれる注射器に似た器具(注入器)を使って耳の穴に樹脂を流していくと、耳のくぼみに沿って樹脂が広がっていく。
数分すると樹脂が固まる。耳型は耳に徐々に空気を入れながら回転させるようにして取り出す。つるんとした触り心地で耳に樹脂は残らず、するりと抜ける。最後にもう一度拡大鏡で耳の中を確認する。耳あな採型はこれで完了。通常のフローだと、出来上がった耳型は採型した販売店からメーカーに送られ、この形状にもとづいた補聴器が作成される。
記者も模型を借りて樹脂の流し込みを体験してみたが、想像しているようにはうまくいかない。綿球をどの位置まで押し込めばいいのかわからなかったり、時間が経って樹脂が固まり耳のくぼみにきちんと沿わなかったり、訓練に裏打ちされた熟練した技術がなければ、きちんとした耳型を採型することはできない。この後の製作フローはすべて耳型をもとに行っていくので、できるだけ完璧な仕上がりが求められるのだ。
採型した耳型
オーダーシートをもとに耳型のトリミングを行う
成形された耳型は3Dスキャナーで読み取り、そのデータからシェルと呼ばれる補聴器のケースを設計していく。シェルの形状を最適化していくのはもちろんだが、補聴器の本体となる基板やベント(通気穴)の位置も同時に調整していく。ここでも作業は一定のパターンに当てはめるのではなく、個々人に合わせて専門家がコンマミリ単位で整える。
3Dスキャナーでデータを読み取り、専門家がモデリングしていく
モデリングデータが仕上がったら、次はいよいよ実機の製作に移る。シェルは同じラボ内にある3Dプリンターを用い、2時間程度で完成する。大量のシェルは識別できるようにレーザーでシリアルナンバーを刻印する。それぞれ形状が異なるので、この工程も1個ずつ手作業で行う必要があるそうだ。
3Dプリンターでシェルを作成
シェルへのシリアルナンバーの刻印後は、まずフェイスプレートという円状の板に電子部品を取り付けていく。これが耳あな型補聴器の外側=ふたの部分となる。非常に繊細な作業となるため、顕微鏡と精密作業用のピンセットを使用する。組み上がったフェイスプレートと基板はシェルにセットしていくのだが、ここでも細かい調整が必要になる。少しでもバランスが悪いと、内部でハウリングする恐れがあるためだ。スタッフは聴診器を使い自分の耳で音を聴きながら、完璧な状態になるまでバランスを整えていく。
基板のはんだづけと音響調整の様子
これでほぼ完成と思いきや、まだ工程は残っている。フェイスプレートから本体をシェルの大きさにあわせて削り出すのだが、ここでも装着感や聴こえやすさを最適にするためにスタッフが形状を少しずつ削って微調整する。その後、補聴器を取り出しやすくするためのテグスを付け、コーティング。シェル表面に気泡や傷はないか、音響特性も評価し、徹底した品質確認が行われ、ようやく出荷可能な状態となる。
仕上げ作業でもまだ調整は続く
オーダーメイドとはいえ、ほとんどの工程はオートメーション化されているのだろうと考えていたが、実際はほとんどが人の手を介して行われていた。しかも、どの工程も気が抜けるものではなく、専門知識と技術があってはじめて可能になる、見ているだけでめまいがしそうな細かい作業ばかりだった。
手間のかかる工程を経て完成した補聴器
また、1台の補聴器が完成するまでに何人もの専門家の手にわたり、調整に次ぐ調整、確認に次ぐ確認が行われていることも印象的だった。小さいゆえに軽く捉えてしまうが、場合によっては生活の安全を左右しかねない補聴器。その責任の重みを、実際に補聴器が生まれる場所から感じ取れた。(BCN・大蔵 大輔)
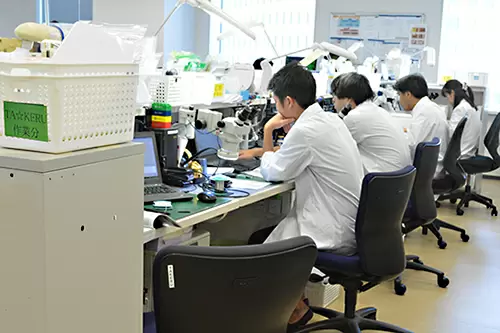
最初の一歩は耳型採型 外耳道まで樹脂で形状把握
補聴器には、耳かけ型、ポケット型など、さまざまな形状のタイプがあるのだが、今回は耳あなにすっぽりと入れて使用する耳あな型を取り上げる。耳あな型はオーダーメイドが基本なので、購入時にはユーザーの耳型を採型する必要がある。通常は補聴器専門店の熟練したスタッフが、必ず耳の病歴や傷が無いかなどの確認を行った後で耳型を採るものだが、今回は特別にオーティコン補聴器で耳の模型を使ってその方法をレクチャーしてもらった。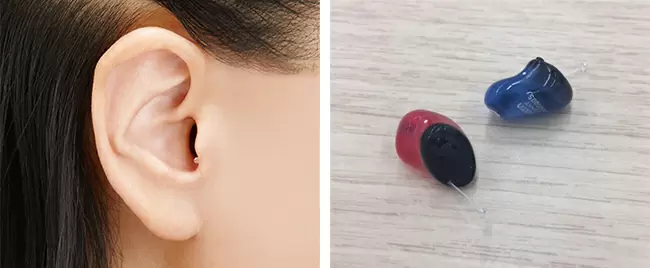
耳型採型は、補聴器を自分の耳に完璧にフィットさせるために行う。装着感はもちろんだが、音を明瞭に聞き取るという目的を達成するためには音の出力口がまっすぐ鼓膜を向いていなければならない。したがって、耳あな型の補聴器は目に見えている表面だけではなく、鼓膜へと続く外耳道まで型をとる。
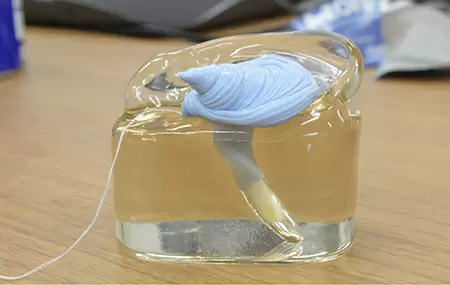
手順としては、まず耳の中を拡大鏡やペンライトで観察する。異常がなければ、次は外耳道の奥に綿球を入れ、耳型の元となる印象材(シリコン樹脂)が耳の奥に入らないように栓をする。今回、印象材は主材と硬化剤の2種類を混ぜ合わせたものを使用した。単体では粘土のような柔らかさだが、混ざると徐々に硬化していく。固まる前にシリンジと呼ばれる注射器に似た器具(注入器)を使って耳の穴に樹脂を流していくと、耳のくぼみに沿って樹脂が広がっていく。
数分すると樹脂が固まる。耳型は耳に徐々に空気を入れながら回転させるようにして取り出す。つるんとした触り心地で耳に樹脂は残らず、するりと抜ける。最後にもう一度拡大鏡で耳の中を確認する。耳あな採型はこれで完了。通常のフローだと、出来上がった耳型は採型した販売店からメーカーに送られ、この形状にもとづいた補聴器が作成される。
記者も模型を借りて樹脂の流し込みを体験してみたが、想像しているようにはうまくいかない。綿球をどの位置まで押し込めばいいのかわからなかったり、時間が経って樹脂が固まり耳のくぼみにきちんと沿わなかったり、訓練に裏打ちされた熟練した技術がなければ、きちんとした耳型を採型することはできない。この後の製作フローはすべて耳型をもとに行っていくので、できるだけ完璧な仕上がりが求められるのだ。
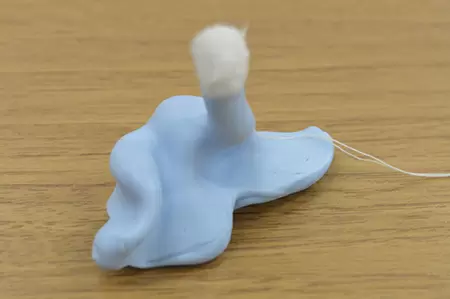
作製はほとんどが手作業 専門家が微調整を繰り返す
オーティコン補聴器の補聴器作製の現場は「工場」ではなく「ラボ」と呼ばれ、その名の通り、研究室のような雰囲気だ。専門店から到着した耳型はそのままで使用できるわけではない。細かい仕様が表記されたオーダーシートをもとに専門技術をもつスタッフが手作業で調整していく。不要な部分は取り除き、逆に足りない部分は補填する。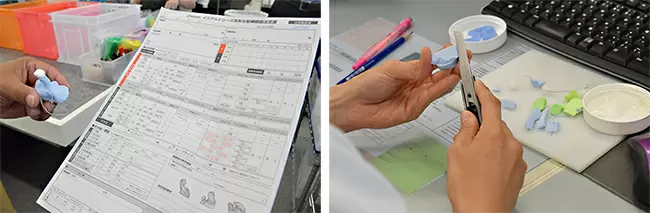
成形された耳型は3Dスキャナーで読み取り、そのデータからシェルと呼ばれる補聴器のケースを設計していく。シェルの形状を最適化していくのはもちろんだが、補聴器の本体となる基板やベント(通気穴)の位置も同時に調整していく。ここでも作業は一定のパターンに当てはめるのではなく、個々人に合わせて専門家がコンマミリ単位で整える。
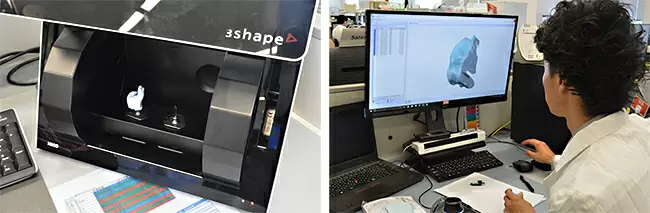
モデリングデータが仕上がったら、次はいよいよ実機の製作に移る。シェルは同じラボ内にある3Dプリンターを用い、2時間程度で完成する。大量のシェルは識別できるようにレーザーでシリアルナンバーを刻印する。それぞれ形状が異なるので、この工程も1個ずつ手作業で行う必要があるそうだ。
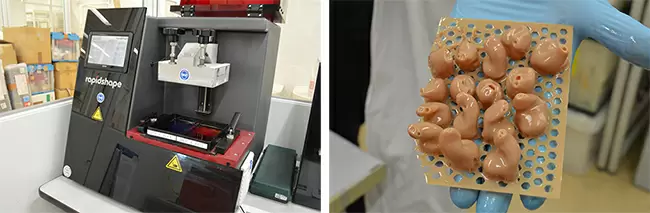
シェルへのシリアルナンバーの刻印後は、まずフェイスプレートという円状の板に電子部品を取り付けていく。これが耳あな型補聴器の外側=ふたの部分となる。非常に繊細な作業となるため、顕微鏡と精密作業用のピンセットを使用する。組み上がったフェイスプレートと基板はシェルにセットしていくのだが、ここでも細かい調整が必要になる。少しでもバランスが悪いと、内部でハウリングする恐れがあるためだ。スタッフは聴診器を使い自分の耳で音を聴きながら、完璧な状態になるまでバランスを整えていく。
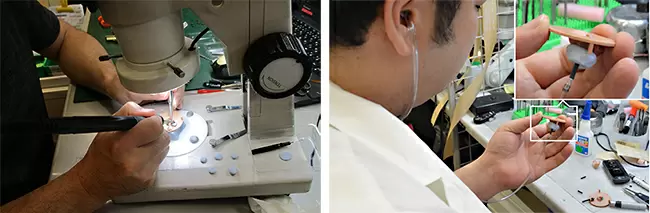
これでほぼ完成と思いきや、まだ工程は残っている。フェイスプレートから本体をシェルの大きさにあわせて削り出すのだが、ここでも装着感や聴こえやすさを最適にするためにスタッフが形状を少しずつ削って微調整する。その後、補聴器を取り出しやすくするためのテグスを付け、コーティング。シェル表面に気泡や傷はないか、音響特性も評価し、徹底した品質確認が行われ、ようやく出荷可能な状態となる。
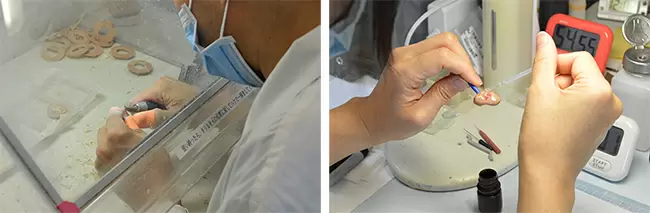
オーダーメイドとはいえ、ほとんどの工程はオートメーション化されているのだろうと考えていたが、実際はほとんどが人の手を介して行われていた。しかも、どの工程も気が抜けるものではなく、専門知識と技術があってはじめて可能になる、見ているだけでめまいがしそうな細かい作業ばかりだった。
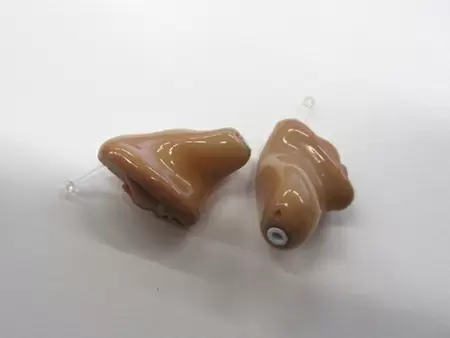
また、1台の補聴器が完成するまでに何人もの専門家の手にわたり、調整に次ぐ調整、確認に次ぐ確認が行われていることも印象的だった。小さいゆえに軽く捉えてしまうが、場合によっては生活の安全を左右しかねない補聴器。その責任の重みを、実際に補聴器が生まれる場所から感じ取れた。(BCN・大蔵 大輔)